Inventory Levels always need to be managed rigorously to ensure there are no outages. If not, how are you going to explain that you’re out of your hottest product to your customers? You can probably think of plenty of reasons or excuses, but that’s not the point! ERPLY understands that as a business owner, there are so many things going on that sometimes you do not know where your inventory goes or how fast it’s flying off the shelves. This is where ERPLY’s stock replenishment system comes in. When it comes to
inventory management, you want to define the “Hey! You’re running low!” level for each product, or simply the warning level. In ERPLY, it’s called the Reorder Point, the minimum or lowest stock level of an item to hold before an order is made with your suppliers to bring the stock up to its Restock Level, which is the maximum amount you would like to order back up to.
Want to use the Reorder Point/Restock Level inventory feature en masse? Our Stock Replenishment Report has you covered. This convenient report highlights all items below your reorder points in red. An item’s stock level below the Reorder Point will trigger you to order more in the Stock Replenishment Report making it easy for you to get a glance of what items are nearing their reorder points and what items are below the reorder point in order to avoid shortages in your stores.
The best part of it? Check all items in red or below the reorder points and you can create Purchase Orders, sorted by the supplier, for all of those items on the fly. Do you have a warehouse or multiple stores locations with higher inventory levels? Rather than generate a PO, you can create a transfer order from one location to the next allowing for full flexibility. You have the ability to set different reorder points and restock levels for each of your locations. We understand not all stores are alike in their selling patterns and demographics of their customers. You determine the points and levels for each location based on how well items are selling specifically there. Reorder Points and Restock Levels can be set manually in the product card or it can also be set in bulk through an import from your excel data. Therefore if you’re editing or adding hundreds or thousands of items, importing will make the process quick, easy, and painless so you can focus on other parts of your business.
Here’s an example of how reordering and restocking work through the Stock Replenishment Report.
Example: I’m selling Apples in my New York store and I have set my reorder point to 10 and restock level to 50. Currently, I have only 8 Apples in stock in New York.
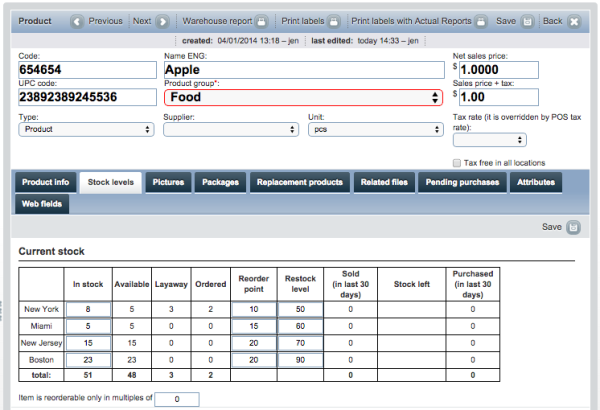
If I run a Stock Replenishment Report for the New York location, the report will display items’ current stock level, items already ordered, sales made during the date range, and stock days. Stock days calculates how many days left you to have until this item’s stock reaches 0 depending on the average sales. The report will highlight any items that are below the reorder point as a warning that you’ll need to order more. Here is an image of what the Stock Replenishment Report looks like in ERPLY:
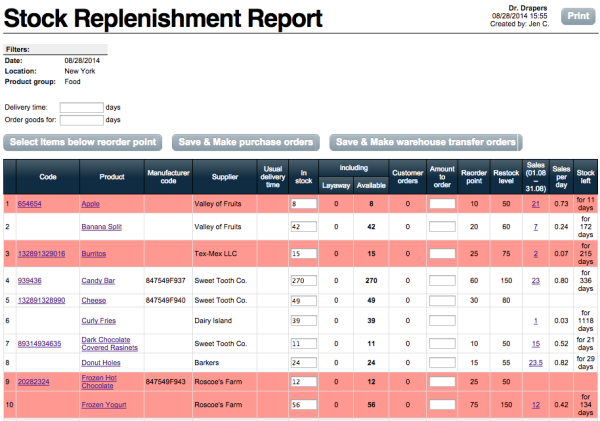
By clicking “Select items below reorder point” button, you will notice that system automatically adds “Amount to order” based on these predefined Restock and Reorder levels. For our example, our reorder point as 10 and restock level as 50. The system shows that Apples have 8 in stock, which is below the reorder point of 10. In order to restock to 50, you must order 42 more Apples.
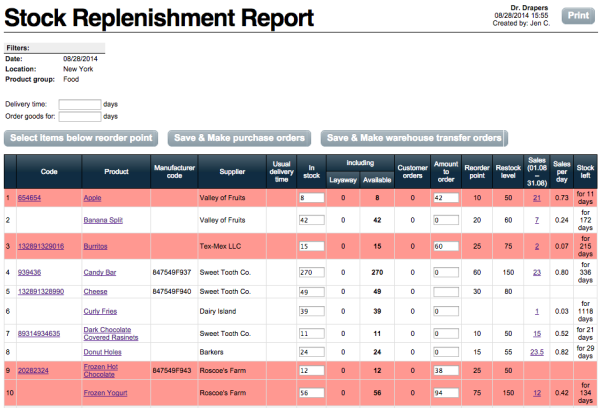
By selecting the button “Save & Make purchase orders”, you can auto-generate Purchase Orders for each supplier. Purchase Orders are created and ready to be sent to your suppliers.
It’s a great way to simplify your inventory procedures and ensure your customers have the optimal experience at the Point of Sale.